3.3 基于MBD技术的全三维设计-工艺-制造协同
MBD(Model-Based-Definition,基于模型的工程定义)技术改变了传统的通过三维模型描述几何形状信息,用二维工程图纸来定义零件尺寸、公差和工艺信息的分步产品数字化定义方法;MBD技术将三维模型作为信息的唯一载体,产品的设计、工艺、制造、检验等都将在三维环境下完成,它的优势可以体现在:
a)提供单源产品定义,消除3D和2D图纸间存在的不一致的潜在风险;
b)减少下游人员(工艺、制造、市场、服务等)对模型的理解时间和偏差;
c)和CAD工具配合使用可以规范、自动化数据集的输入,并进行公差分析;
d)可以在产品开发流程的早期获取设计意图,极大地支持并行工程。
如下图4所示,MBD技术在装配和机加工艺过程中的应用实例:
图4. MBD技术在装配和机加工艺应用示例
3.4 3D体验制造资源库和工艺模板库
Catalog(库)作为工艺协同设计平台重要的组成部分,除包含标准机器人库、人体姿态库等常用资源库之外,还能够方便创建和管理多种类型对象的库文件,从而实现知识和经验的积累,加速工艺设计过程;工艺路线模板和加工特征模板对同一类型或具有相似加工特征的零部件,建立典型工艺路线模板和特征模板,如图5所示,工艺设计过程中实现快速调用;
图5. 典型工艺模板
4、3D体验数字化制造解决方案及案例说明
如前文所述,工艺部门从3D体验协同平台中获取到经过设计评审和工艺会签后正式发布的三维模型和EBOM数据,在3D体验环境中开展工艺规划和设计。如下图6所示,装配工艺人员首先根据产品的工艺属性,在EBOM和三维模型的基础上进行BOM重构:去除虚拟件、增加工艺组件,定义零部件的装配顺序、操作工步的内容,分配场地或者工位资源,增加工艺物料等信息,BOM重构的过程包含了PBOM、工艺路线和MBOM的形成。对于单个零件,加工工艺路线可能需要包含毛坯材料准备、热处理、数控加工等多道工序步骤,工艺人员可以根据任务分工,细化相关的工艺节点。图6. 3D体验工艺设计和规划解决方案
在工艺设计和规划的基础上,工艺人员继续开展工艺仿真、工时分析、线平衡等工作。接下来,本章将对3D体验数字化制造装配工艺流程举例说明。
4.1 根据EBOM和3D数模进行BOM重构,创建初始MBOM(或称之为PBOM)
工艺人员在DELMIA窗口中搜索和加载产品的EBOM和3D数模(NX、Creo等其它3D CAD软件创建的三维装配和零件模型可以通过达索3D体验数据转换接口直接读入),根据零部件工艺属性创建工艺组/合件,然后通过零件分配工具或手工拖拽的方式将零件分配到对应的工艺组件中,如下图7所示,形成3D可视化装配工艺结构树,PPR数据模型树中EBOM和初始MBOM并列。
图7. 3D体验初始MBOM创建
4.2 创建和编辑工艺路线
EBOM重构形成了初始的MBOM,工艺人员结合企业内部制造场地(site)和工位资源(station)的分布情况,将制造组件和零部件分别分配到对应的场地资源上去;如下图8所示,将其中的一个装配组件分配到两个site上进行分装和总成,形成了产品的装配工艺路线;对于零件加工工艺路线,可以在工艺分工之后进一步细化,如材料准备、热处理、数控加工等工序步骤。此处的Site是Logical对象,在PPR数据模型中代表物理场地和工位。
图8. 3D体验工艺路线编辑4.3 分发和接收工艺任务
产品的装配工艺路线在3D体验平台中定义完成之后,还需要将不同专业的工作分配到专门的工程师负责,并能够监控工艺的进展情况;在此可以将DELMIA创建的工艺路线自动转换为项目WBS任务,同时,工艺任务和负责人等属性都自动与WBS关联;如下图9所示,在ENOVIA窗口中可以分发和监控任务的完成进度,当用户登录接收到通知系统时,可以查看自己的任务节点。
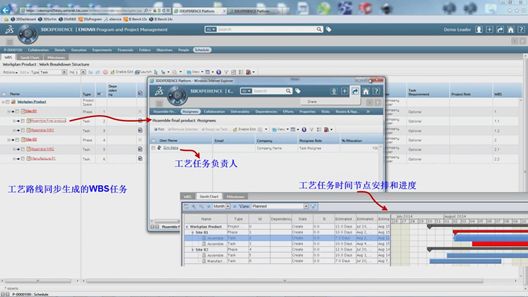
图9. 3D体验工艺任务分发和管理
4.4 详细工艺设计和仿真验证
工艺人员接收到任务,在DELMIA窗口中加载相关的产品数模和工序信息,估算工时并完成负载平衡分析,然后可以调入工装和夹具三维数模,仿真验证各零部件的装配路径,确定产品装配工艺顺序,如下图10所示。
图10. 3D体验装配工艺仿真验证
4.5 文档工艺输出
如下图11所示,针对工序步骤的每一步操作,工艺人员可以在DELMIA窗口添加工序说明、技术附图、文档,现场需要采集的工艺数据、交验要求等信息,通过定制模板格式输出当前步骤的3D作业指导。对于热处理和材料准备等二维工艺卡片,也可以根据格式要求定制输出。
图11. 3D体验工艺文档输出
4.6 工艺设计审批
如下图12所示,3D体验平台项目工艺任务WBS节点可以关联工艺任务和工艺文档等交付件,当工艺人员完成所负责的工艺任务后,包括详细工艺设计产生的PPR模型文件和作业指导等工艺文档都以交付物的形式关联到任务节点,通过进行审批和发放流程来提升PPR模型及工艺文档的生命周期状态;当所有相关交付件审批完成后,工艺任务也提升为“完成”状态。
图12. 3D体验工艺任务审批
5、结束语
在并行设计制造一体化的背景下,企业需要建立跨越时间和空间的数字化协同平台,让分布的设计和制造团队共享协同工作模式,利用数字化平台实现企业内部和企业之间不同区域多个开发小组之间的分工协作,不同厂家、外部合作伙伴之间的协作。达索3D体验数字化协同平台的推广应用正在逐步开展,希望能有更多的用户来挖掘深层次的价值。
关键词:3D体验平台、3DExperience、达索软件、数字化制造